7.4. В отдельных отраслях промышленности при проведении капитальных ремонтов строительных конструкций возможны простои размещенного в производственных зданиях технологического оборудования. Это вызывает неполное использование основных фондов предприятия и соответствующие народнохозяйственные потери (косвенные потери от коррозии).
Величина указанных в последнем члене формулы (2) потерь от простоя оборудования Сп.о. может быть определена по формуле
Сп.о. = Ен Коб Тп.об, (4)
где Ен - нормативный коэффициент эффективности капитальных вложений; Коб - проектная стоимость технологического оборудования или машин, простаивающих при капитальном ремонте строительных конструкций (принимается по табл. 4 прил. 12); Тп.об - время в годах, в течение которого простаивает основное технологическое оборудование цеха (принимается условно равным продолжительности капитального ремонта конструкции (см. табл. 3 прил. 12).
Поскольку расчеты приведенных затрат по сравниваемым вариантам антикоррозионной защиты проводятся на натуральную единицу измерения конструкций, необходимо иметь соответствующие технические проектные данные. Для предварительных расчетов рекомендуется использовать приведенные в табл. 29 усредненные показатели по сборным железобетонным конструкциям одноэтажного производственного здания.
Таблица 29
Конструкции |
Объем сборных конструкций, в м3 на 1 м2 здания |
Площадь здания, в м2 на 1 м3 бетона конструкции |
элементы фундаментов |
0,04 |
25 |
Колонны, стойки |
0,015 |
67 |
Подстропильные фермы и балки |
0,02 |
50 |
Стропильные фермы и балки |
0,03 |
33 |
Плиты покрытий |
0,06 |
17 |
Стеновые панели |
0,02 |
50 |
Использование усредненных показателей позволяет на предварительной стадии проектирования оценить наиболее экономичный вариант антикоррозионной защиты или определить оптимальные межремонтные сроки службы строительных конструкций при минимуме приведенных затрат. Стоимость используемых при антикоррозионной защите строительных конструкций материалов и изделий может быть уточнена по действующим прейскурантам оптовых цен.
7.5. На стадии рабочего проектирования уточнение экономической эффективности защиты конструкций от коррозии достигается за счет увеличения количества учитываемых технико-экономических параметров.
Конкретизируются принятые объемно-планировочные и конструктивные решения, назначение проектируемого предприятия, характер и годовой объем выпускаемой им продукции, территориальное расположение объекта и поставщиков строительных конструкций и материалов, механовооруженность строительной или ремонтно-строительной организации, применяемые средства механизации монтажных и антикоррозионных работ и т. п.
В составе эксплуатационных затрат дополнительно учитываются затраты на текущие ремонты строительных конструкций, ежегодные затраты по обслуживанию специальных средств защиты и техническому содержанию зданий и сооружений. Расширяется круг учитываемых прямых и косвенных потерь от коррозии строительных конструкций.
Технико-экономические обоснования выбора эффективного варианта защиты от коррозии должны базироваться на соответствующих расчетах, выполняемых по «Руководству по определению экономической эффективности повышения качества и долговечности строительных конструкций» (М.: Стройиздат, 1981), методическим материалам СЭВ по стандартизации «Защита от коррозии в строительстве. Методы определения экономической эффективности» (ММ 6-83), «Защита от коррозии в строительстве. Метод определения экономических потерь» (ММ 10-85). Ниже приводятся примеры технико-экономических расчетов.
Пример 1. Требуется определить экономическую эффективность антикоррозионной защиты поверхности железобетонных стропильных балок одноэтажного промышленного здания на предварительной стадии проектирования.
Общая производственная площадь здания химического производства 10000 м2, степень агрессивного воздействия среды -среднеагрессивная, срок строительства здания - 2 года, нормативный срок службы здания - 80 лет. Балка двутаврового сечения пролетом 12 м по серии 1.462-1 (вып. 1), под расчетную нагрузку 65 МПа, объем бетона 2 м3, общий расход стали - 242 кг, площадь поверхности балки, защищаемая лакокрасочным покрытием, - 20 м.
Система антикоррозионной зашиты балок лакокрасочными покрытиями представлена в двух вариантах:
1 - защитное нетрещиностойкое химически стойкое покрытие из одного слоя грунтовки лаком ХВ-784 толщиной 15 мкм (расход лака 0,194 кг/м2) и семи покрывных слоев эмалью ХВ-785 с общей толщиной покрытия 140 мкм (расход эмали 1,13 кг/м2).
2 - защитное трещиностойкое покрытие из двух слоев грунтовки лаком ХП-734 толщиной 30 мкм (расход лака 0,4 кг/м2) и восьми покрывных слоев эмалью ХП-799 (расход эмали 1,3 кг/м2).
Способ нанесения лакокрасочных покрытий в обоих вариантах ѕ пневматическое напыление пистолетом-краскораспылителем 0-45.
Трещиностойкое покрытие на основе хлорсульфированного полиэтилена ХП обладает большими защитными свойствами и позволяет увеличить межремонтный срок службы конструкций (до 30 лет).
По табл. 26 и 27 ориентировочные сроки службы защитных лакокрасочных покрытий для среднеагрессивной среды составляют Тз.к.1 = 4 года и Тз.к.2 = 7 лет, а периодичность капитальных ремонтов Тк.р.1 = 23 года и Тк.р.2 = 30 лет.
Так как в сравниваемых вариантах защиты применяемые материалы отличаются по виду и расходу, определяем приведенные капитальные вложения в производство лакокрасочных материалов с учетом их расхода на одну балку (20 м2 поверхности), коэффициента эффективности капитальных вложений (Ен = 0,15) и данных удельных капитальных вложений по табл. 1 прил. 12 (пп. 3.2 и 3.4; пп. 3.3 и 3.5):
См(с)1 = 0,15Ч20Ч0,715Ч0,194 + 0,15Ч20Ч0,725Ч1,13 = 2,88 руб.;
См(с)2 = 0,15Ч20Ч0,875Ч0,4 + 0,15Ч20Ч0,9Ч1,3 = 4,56 руб.
Стоимость стропильной балки «в деле» (без защиты от коррозии) принимаем по п. 1.3 табл. 1 прил. 12:
Сд1 = Сд2 = 106 руб.
Проектную стоимость лакокрасочной защиты в зависимости от вида материалов принимаем по табл. 1 прил. 12 (пп. 3.2 и 3.4; пп. 3.3 и 3.5) с учетом расхода материалов и площади защиты (20 м2):
Сз1 = 20 (0,194Ч0,6 + 1,13Ч0,79) = 20,18 руб.;
Сз2 = 20 (0,4Ч0,735 + 1,3Ч1) = 31,88 руб.
Народнохозяйственные потери от простоя расположенного в здании технологического оборудования определяем по формуле (4), пользуясь данными табл. 29 и прил. 12.
По табл. 4 прил. 12 ориентировочная стоимость технологического оборудования для предприятий химической промышленности на 1 м2 общей площади производственных зданий Коб = 148 руб.
По табл. 29 на 1 м2 бетона подстропильных балок приходится 50 м2 производственной площади здания, т.е. в рассматриваемом примере на одну балку (объемом 2 м3) приходится 100 м2 площади здания. По табл. 3 прил. 12 ориентировочная продолжительность капитального ремонта балок на 1 м3 бетона конструкции составляет 0,013 года, т.е. в нашем случае (при объеме бетона в балке 2 м3) равна 0,026 года.
Таким образом, величина потерь по формуле (4) составляет
Спо = 0,15Ч148Ч100Ч0,026 = 57,72 руб.
Обобщенные исходные параметры для расчета экономического эффекта на одну балку приведены в табл. 30.
Таблица 30
Показатели |
Размерность |
Вариант 1 |
Вариант 2 |
1. Коэффициент эффективности капитальных вложений Ен |
- |
0,15 |
0,15 |
2. Норматив приведения разновременных затрат Е |
ѕ |
0,1 |
0,1 |
3. Приведенные капитальные вложения в сопряженные отрасли См(с) |
руб. |
2,88 |
4,56 |
4. Стоимость антикоррозионной защиты балки лакокрасочными покрытиями Сз |
» |
20,18 |
31,88 |
5. Расчетная стоимость балки «в деле» без защиты от коррозии Сд |
» |
106 |
106 |
6. Нормативный срок строительства объекта |
лет |
2 |
2 |
7. Срок службы здания Тс |
» |
80 |
80 |
8. Затраты на капитальный ремонт по табл. 2 прил. 12 Ск.р. = Сд0,55 +Сз1,25 |
руб. |
83,53 |
98,15 |
9. Периодичность проведения капитальных ремонтов |
лет |
23 |
30 |
10. Затраты на возобновление антикоррозионной лакокрасочной защиты по табл. 2 прил. 12 Сз.к. = Сз1,25 |
руб. |
25,23 |
39,85 |
11. Периодичность возобновления (срок службы) лакокрасочной защиты |
лет |
4 |
7 |
12. Потери от простоя основного технологического оборудования во время проведения капитального ремонта железобетонной балки Сп.о |
руб. |
57,7 |
57,7 |
13. Количество балок на общую площадь проектируемого цеха А2 |
шт. |
100 |
100 |
Приведенные затраты, осуществляемые до начала эксплуатации по сравниваемым вариантам с учетом фактора времени и срока строительства объекта 2 года (at = 1,21) равны:
Зн1 = (2,88 + 106 + 20,18)Ч1,21 = 156,16 руб.
Зн2 = (4,56 + 106 + 31,88)Ч1,21 = 172,35 руб.
Приведенные затраты в процессе эксплуатации с учетом фактора времени при значениях 1/at, принимаемых по табл. 28, равны:
Для варианта 1
Количество капитальных ремонтов gк.р. - 1 = 80/23-1 = 3, т.е. по табл. 28: 1/a23 = 0,111; 1/a46 = 0,012 и 1/a69 = 0,002.
Затраты на капитальные ремонты, приведенные к началу эксплуатации: = 83,53 (0,111 + 0,012 + 0,002) = 83,53Ч0,125 = 10,44 руб.
Количество возобновлений лакокрасочных покрытий при сроке службы Тз.к. = 4 годам: gз.к. - 1 = 80/4 - 1 = 19.
Затраты на возобновление антикоррозионной защиты с учетом 1/at по табл. 28, приведенные к началу эксплуатации:
= 25,23 (0,683 + 0,466 + 0,318 + 0,217 + 0,148 + 0,101 + 0,069 + 0,047 + 0,032 + 0,022 + 0,015 + 0,01 + 0,007 + 0,004 + 0,002 +0,002 + 0,002 + 0,001 + 0,001) = 25,23Ч2,147 = 54,17 руб.
Сумма потерь от простоя технологического оборудования цеха во время капитальных ремонтов балки, приведенная к началу эксплуатации = 57,7 (0,111 + 0,012 + 0,002) = 57,7Ч0,125 = 7,21 руб.
Для варианта 2
Количество капитальных ремонтов gк.р. - 1 = 80/30 - 1 = 2, т.е. по табл. 28 1/a30 = 0,057 и 1/a60 = 0,002.
Затраты на капитальные ремонты, приведенные к началу эксплуатации: = 98,l5 (0,057 + 0,002) = 5,79 руб.
Количество возобновлений лакокрасочной защиты gз.к. - 1 = 80/7 ѕ 1 = 11.
Затраты на возобновление защиты, приведенные к началу эксплуатации, с учетом коэффициентов 1/at (по табл. 28 при Тз.к. = 7 годам: = 39,85 (0,513 + 0,263 + 0,135 + 0,069 + + 0,035 + 0,018 + 0,009 + 0,004 + 0,002 + 0,001 + 0,001) = 39,85Ч1,05 = 41,84 руб.
Для облегчения и ускорения расчетов суммарные коэффициенты приведения разновременных затрат S1/at = m в зависимости от срока службы здания Тс и срока службы антикоррозионной защиты Та.к. приведены в табл. 5 прил. 12.
В рассматриваемом случае при Тс = 80 лет и Тз.к. = 7 лет по табл. 5 прил. 12 m = 1,05.
Сумма потерь от простоя технологического оборудования = 57,7 (0,057 + 0,002) = 3,4 руб.
Таким образом, суммарные приведенные затраты по сравниваемым вариантам защиты по формуле (8) равны:
З1 = 156,l6 + 10,44 + 54,17 + 7,21 = 227,98 руб.;
З2 = 172,35 + 5,79 + 41,84 + 3,4 = 223,38 руб.
Экономический эффект на 1 балку
Э = З1 З2 = 227,98 - 223,38 = 4,6 руб., или 0,23 руб/м3 поверхности.
Экономический эффект на проектируемое здание цеха по формуле (1) при количестве балок 100 шт. составляет
Эз.д. = (227,98 223,38)Ч100 = 460 руб.
Пример 2. Требуется определить эффективность применения комплексной добавки в бетон, повышающей морозостойкость бетона и долговечность железобетонных конструкций.
Для повышения межремонтных сроков службы свайной эстакады морского причала рекомендуется при изготовлении свай применить комплексную добавку в бетон (50 % эмульсии ГКЖ-94 и сульфитно-дрожжевой бражки - СДБ).
Совместное введение в бетонную смесь кремнийорганического полимера ГКЖ-94 и пластификатора СДБ позволяет уменьшить водоцементное отношение при сохранении требуемой подвижности смеси, повысить морозостойкость бетона и долговечность железобетонных конструкций.
За исходный вариант принимается конструкция причала аналогичных размеров и прочности с опорами из железобетонных свай, изготавливаемых по традиционной технологии без введения добавок в бетон.
Исходные данные для расчета (на 100 м причала)
Расчеты проводятся по методическому материалу СЭВ (ММ 6-83) с использованием табл. 28 и прил. 12 настоящего Пособия.
Исходные данные для расчета приведены в табл. 31.
Таблица 31
Наименование показателей |
Единица измерения |
Вариант 1 (без добавки) |
Вариант 3 (с добавкой) |
Нормативный срок службы (эксплуатации) причала, Тс |
год |
50 |
50 |
Период между началом строительства причальной эстакады и вводом ее в эксплуатацию |
» |
1 |
1 |
Капитальные вложения в химическую промышленность (на производство комплексной добавки), Зм(с) |
руб. |
- |
97,59 |
Норматив для приведения разновременных затрат, Е |
- |
0,1 |
0,1 |
Расчетная себестоимость строительства причала, Сд |
руз. |
350606 |
351341 |
Периодичность капитальных ремонтов, Тк.р |
год |
15 |
20 |
Затраты на один капитальный ремонт причала, Ск.р |
руб. |
78886 |
81752 |
Среднегодовые затраты на текущие ремонты, Ст.р |
» |
935 |
562 |
Расходы на 1 судносутки простоя сухогрузных судов универсального назначения |
» |
515 |
515 |
Продолжительность одного капитального ремонта |
лет/сут |
0,27/100 |
0,27/100 |
Годовой объем строительства причалов |
м |
500 |
500 |
1. Расчет приведенных затрат, осуществляемых до начала эксплуатации причала, производится по формуле (3) MM 6-83 при
at = l,l:
Зн1 = (350606 + 0)Ч1,1 = 385666,6 руб.;
Зн2 = (351341 + 97,59)Ч1,1 = 386582 руб.
2. Расчет приведенных затрат, осуществляемых при эксплуатации причала, производится по формуле (7) MM 6-83, табл. 28 и табл. 5 прил. 12 настоящего Пособия:
= 78886 (1/a15 + 1/a30 + 1/a45) = 78886 (0,239 + 0,057 + 0,013) = 78886Ч0,309 = 24375,8 руб.;
= 81752 (1/a20 + 1/a40) = 81752 (0,148 + 0,022) = 81752Ч0,17 = 13897,8 руб.;
= 935Ч9,9 = 9256,5 руб. (табл. 5 прил. 12 при Тс = 50 лет и Тт.р = 1 году).
= 562Ч9,9 = 5563,8 руб. (табл. 5 прил. 12 при Тс = 50 лет и Тт.р = 1 году).
Потери от простоя судов при капитальных ремонтах причала:
= 0,15Ч515Ч100Ч0,309 = 2387 руб.;
= 0,15Ч515Ч100Ч0,17 = 1313,3 руб.
3. Суммарные приведенные затраты по сравниваемым вариантам на 100 м причала:
З1 = 385666,6 + (24375,8 + 9256,5 +2387) =421685,9 руб.;
З2 = 386582,5 + (13897,8 + 5563,8 +1313,3) = 407357,4 руб.
4. Годовой экономический эффект от применения комплексной добавки в бетон на 500 м причала
Эг = (421685,9 - 407357,4)5 = 71642,5 руб.
ПРИЛОЖЕНИЕ 1(1)
Группы агрессивных газов в зависимости от их вида и концентрации
Наименование |
Концентрация, мг/м3, для групп газов |
|
А |
в |
С |
D |
Углекислый газ |
До 2000 |
Св. 2000 |
ѕ |
ѕ |
Аммиак |
» 0,2 |
Св. 0,2 до 20 |
Св. 20 |
- |
Сернистый ангидрид |
До 0,5 |
Св. 0,5 до 10 |
Св. 10 до 200 |
Св. 200 до 1000 |
Фтористый водород |
» 0,05 |
» 0,05 » 5 |
» 5 » 10 |
» 10 » 100 |
Сероводород |
» 0,01 |
» 0,01 » 5 |
» 5 » 100 |
» 100 |
Оксиды азота* |
» 0,1 |
» 0,1 » 5 |
» 5 » 25 |
» 25 » 100 |
Хлор |
» 0,1 |
» 0,1 » 1 |
» 1 » 5 |
» 5 » 10 |
Хлористый водород |
» 0,05 |
» 0,05 » 5 |
» 5 » 10 |
» 10 » 100 |
* Оксиды азота, растворяющиеся в воде с образованием растворов кислот.
Примечание. При концентрации газов, превышающей пределы, указанные в гр. «D» настоящей таблицы, возможность применения материала для строительных конструкций следует определять на основании данных экспериментальных исследований. |
ПРИЛОЖЕНИЕ 2(2)
Характеристика твердых сред
(солей, аэрозолей и пыли)
Растворимость твердых сред в воде и их гигроскопичность |
Наиболее распространенные соли, аэрозоли, пыли |
Малорастворимые |
Силикаты, фосфаты (вторичные и третичные) и карбонаты магния, кальция, бария, свинца; сульфаты бария, свинца; оксиды и гидроксиды железа, хрома, алюминия, кремния |
Хорошо растворимые малогигроскопичные |
Хлориды и сульфаты натрия, калия, аммония; нитраты калия, бария, свинца, магния; карбонаты щелочных металлов |
Хорошо растворимые гигроскопичные |
Хлориды кальция, магния, алюминия, цинка, железа; сульфаты магния, марганца, цинка, железа; нитраты и нитриты натрия, калия, аммония; все первичные фосфаты; вторичный фосфат натрия; оксиды и гидроксиды натрия, калия |
ПРИЛОЖЕНИЕ 3
Упругость паров воды над насыщенными водными растворами хорошо растворимых солей при 20°С
Наименование растворов |
Давление паров воды в |
Равновесная относительная |
Растворимость в 100 г воды при |
Гигроскопичность |
солей |
Па |
мм рт. ст. |
влажность, % |
20 °С |
|
ZnCl2 |
233,3 |
1,75 |
10 |
367 |
Гигроскопичные |
CaCl2 |
819,9 |
6,15 |
35 |
74,5 |
» |
Zn(NО3)2 |
981,2 |
7,36 |
42 |
118,8 |
» |
NH4NO3 |
1565,2 |
11,74 |
67 |
192 |
Малогигроскопичные |
NaNO3 |
1803,8 |
13,53 |
77 |
87,5 |
То же |
NaCl |
1817,2 |
13,63 |
78 |
35,9 |
» |
NH4Cl |
1855,8 |
13,92 |
79 |
37,5 |
» |
Na2SO4 |
1893,2 |
14,2 |
81 |
19,2 |
» |
(NH4)2SO4 |
1895,8 |
14,22 |
81 |
76,3 |
» |
KCl |
2005,2 |
15,04 |
86 |
34,4 |
» |
CuSO4 |
2086,5 |
15,65 |
89 |
76,4 |
» |
ZnSO4 |
2123,8 |
15,93 |
91 |
54,1 |
» |
KNO3 |
2167,8 |
16,26 |
93 |
31,6 |
» |
K2SO4 |
2306,5 |
17,3 |
99 |
11,1 |
» |
CaSО4 |
ѕ |
ѕ |
ѕ |
0,20 |
» |
Примечание. При значениях относительной влажности воздуха, больших равновесной, на поверхности образуется конденсат. |
ПРИЛОЖЕНИЕ 4
А. Метод определения эффективного коэффициента диффузии для углекислого газа в бетоне
Диффузионную проницаемость бетона определяют в зависимости от толщины нейтрализованного слоя и количества углекислого газа, поглощенного бетоном за время хранения образцов в камере с повышенным содержанием углекислого газа при заданной постоянной влажности бетона.
Диффузионная проницаемость бетона определяется на образцах, имеющих форму куба, призмы или пластины, минимальный размер рабочей грани которых должен быть не менее 7 см, а толщина - не менее 3 см. Образцы могут быть изготовлены в форме либо отобраны из конструкций. Количество образцов должно быть не менее 10. Образцы, предназначенные для испытаний, предварительно выдерживают в камере с относительной влажностью воздуха 75±3 % при температуре 20±5°С до установления постоянной массы, после чего изолируют со всех сторон, кроме одной рабочей грани, плотным покрытием, например из парафиноканифольной мастики.
Установка для проведения испытаний должна иметь постоянные параметры газовой среды: концентрацию СО2 10±0,5% по объему, относительную влажность воздуха 75±3 %, температуру 20±5°С. Возможные варианты установок для испытаний представлены в «Руководстве по определению диффузионной проницаемости бетона для углекислого газа» (НИИЖБ, М., 1974).
Образцы выдерживают в камере с углекислым газом не менее 7 сут. и не более того периода, в течение которого образец будет нейтрализован на половину своей толщины.
По истечении заданного срока образцы раскалывают в направлении, нормальном неизолированной грани. На поверхность скола пипеткой наносят 0,1 %-ный раствор фенолфталеина на этиловом спирте.
Мерной линейкой измеряют толщину слоя бетона от поверхности бетона до границы слоя, окрашенного в малиновый цвет. Измерения производят через 1 см по длине кромки образца.
Эффективный коэффициент диффузии углекислого газа в бетоне рассчитывают по формуле в см2/с
D = (moX2)/2Ct,
где mo - Реакционная емкость бетона или объем газа, поглощенного единицей объема бетона; X - среднеарифметическая толщина нейтрализованного слоя бетона, см; С - концентрация углекислого газа в воздухе в относительных величинах по объему; t - продолжительность воздействия газа на бетон, с. Величину реакционной емкости mo рассчитывают по формуле
mo = 0,4Цpf,
где Ц - численно равное содержанию цемента в бетоне, кг/м3; p - количество основных окислов в цементе в пересчете на СаО в относительных величинах по массе, принимается по данным химического анализа цемента; f - степень нейтрализации бетона равная отношению количества основных окислов, прореагировавших с углекислым газом, к общему их количеству в цементе.
Б. Метод определения агрессивной углекислоты
При определении степени углекислой коррозии содержание агрессивной углекислоты в жидкой среде может быть определено экспериментально по отдельной пробе воды или путем вычисления по содержанию свободной углекислоты в общей пробе воды на химический анализ. Содержание агрессивной углекислоты определяют экспериментально в отдельной пробе воды. Пробы воды отбирают в сухую емкость на 250 мл с хорошо подобранной пробкой, в которую предварительно помещено 2 - 3 г химически чистого карбоната кальция. Анализ проводят через 5 - 6 дней (метод Гейера),
Вычисление содержания агрессивной углекислоты проводят по разности между содержанием свободной и равновесной углекислоты.
Концентрация (СО2) свободная, мг/л, согласно требованиям ГОСТ 4979-49, должна быть определена в день отбора пробы воды на анализ.
Количество углекислоты рассчитывают по формуле:
(СО2) равновесной = а[Са2+]+b, где а и b - коэффициенты, зависящие от содержания в воде ионов НСО3 , , Cl ; концентрацию Са2+, мг/л, определяют по таблице.
Значения коэффициентов а и b
Бикарбонатная щелочность |
Суммарное содержание ионов Cl и , мг/л |
мгЧ |
град |
0-200 |
201-400 |
401-600 |
601-800 |
801-1000 |
более 1000 |
экв/л |
|
a |
b |
a |
b |
a |
b |
a |
b |
a |
b |
a |
b |
1,05 |
3 |
0 |
15 |
ѕ |
ѕ |
ѕ |
ѕ |
ѕ |
ѕ |
ѕ |
ѕ |
ѕ |
ѕ |
1,4 |
4 |
0,01 |
16 |
0,01 |
17 |
0,01 |
17 |
0 |
17 |
0 |
17 |
0 |
17 |
1,8 |
5 |
0,04 |
17 |
0,04 |
18 |
0,03 |
17 |
0,02 |
18 |
0,02 |
18 |
0,02 |
18 |
2,1 |
6 |
0,07 |
19 |
0,06 |
19 |
0,05 |
18 |
0,04 |
18 |
0,04 |
18 |
0,04 |
18 |
2,5 |
7 |
0,1 |
21 |
0,08 |
20 |
0,07 |
19 |
0,06 |
18 |
0,06 |
18 |
0,05 |
18 |
2,9 |
8 |
0,13 |
23 |
0,11 |
21 |
0,09 |
19 |
0,08 |
18 |
0,07 |
18 |
0,07 |
18 |
3,2 |
9 |
0,16 |
25 |
0,14 |
22 |
0,11 |
20 |
0,1 |
19 |
0,09 |
18 |
0,08 |
18 |
3,6 |
10 |
0,2 |
27 |
0,17 |
23 |
0,14 |
21 |
0,12 |
19 |
0,11 |
18 |
0,1 |
18 |
4 |
11 |
0,24 |
29 |
0,2 |
24 |
0,16 |
22 |
0,15 |
20 |
0,13 |
19 |
0,12 |
19 |
4,3 |
12 |
0,28 |
32 |
0,24 |
26 |
0,19 |
23 |
0,17 |
21 |
0,16 |
20 |
0,14 |
20 |
4,7 |
13 |
0,32 |
34 |
0,28 |
27 |
0,22 |
24 |
0,2 |
22 |
0,19 |
21 |
0,17 |
21 |
5 |
14 |
0,36 |
29 |
0,32 |
29 |
0,25 |
26 |
0,23 |
23 |
0,22 |
22 |
0,19 |
22 |
5,4 |
15 |
0,4 |
38 |
0,36 |
30 |
0,29 |
27 |
0,26 |
24 |
0,24 |
23 |
0,22 |
23 |
5,7 |
16 |
0,44 |
41 |
0,4 |
32 |
0,32 |
28 |
0,29 |
25 |
0,27 |
24 |
0,25 |
24 |
6,1 |
17 |
0,48 |
43 |
0,44 |
34 |
0,36 |
30 |
0,33 |
26 |
0,3 |
25 |
0,28 |
25 |
6,4 |
18 |
0,54 |
46 |
0,47 |
37 |
0,4 |
32 |
0,36 |
28 |
0,33 |
27 |
0,31 |
27 |
6,8 |
19 |
0,61 |
48 |
0,51 |
39 |
0,44 |
33 |
0,4 |
30 |
0,37 |
29 |
0,34 |
28 |
7,1 |
20 |
0,67 |
51 |
0,55 |
41 |
0,48 |
35 |
0,44 |
31 |
0,41 |
30 |
0,38 |
29 |
7,5 |
21 |
0,74 |
53 |
0,6 |
43 |
0,53 |
37 |
0,48 |
33 |
0,45 |
31 |
0,41 |
31 |
7,8 |
22 |
0,81 |
55 |
0,65 |
45 |
0,58 |
38 |
0,53 |
34 |
0,49 |
33 |
0,44 |
32 |
8,2 |
23 |
0,88 |
58 |
0,7 |
47 |
0,63 |
40 |
0,58 |
35 |
0,53 |
34 |
0,48 |
33 |
8,6 |
24 |
0,96 |
60 |
0,76 |
49 |
0,68 |
42 |
0,63 |
37 |
0,57 |
36 |
0,52 |
35 |
9 |
25 |
1,04 |
63 |
0,81 |
51 |
0,73 |
44 |
0,67 |
39 |
0,61 |
38 |
0,56 |
37 |
10,7 |
30 |
1,44 |
75 |
1,06 |
61 |
0,98 |
54 |
0,87 |
49 |
0,81 |
43 |
0,76 |
47 |
14,3 |
40 |
2,34 |
95 |
1,56 |
81 |
1,48 |
74 |
1,27 |
69 |
1,21 |
68 |
1,16 |
67 |
17,8 |
50 |
3,34 |
120 |
2,16 |
102 |
1,98 |
94 |
1,67 |
79 |
1,61 |
88 |
1,56 |
87 |
21,3 |
60 |
4,44 |
145 |
2,66 |
123 |
2,48 |
114 |
2,17 |
99 |
2,01 |
98 |
1,96 |
97 |
25 |
70 |
5,44 |
165 |
3,16 |
143 |
2,98 |
134 |
2,67 |
119 |
2,41 |
118 |
2,36 |
117 |
28,5 |
80 |
6,54 |
195 |
3,76 |
163 |
3,48 |
154 |
3,07 |
139 |
2,81 |
138 |
2,76 |
137 |
32,1 |
90 |
7,64 |
215 |
4,36 |
183 |
3,98 |
174 |
3,47 |
159 |
3,2 |
148 |
3,16 |
147 |
ПРИЛОЖЕНИЕ 5
Химические добавки, применяемые для повышения коррозионной стойкости
Таблица 1
Условные обозначения добавок и их дозировки
Вид добавок |
Добавки |
Условные обозначения добавок |
Рекомендуемые дозировки добавок* |
1. Воздухововлекающие |
Смола нейтрализованная воздухововлекающая |
СНВ |
0,005 - 0,035 |
|
Клей талловый пековый |
КТП |
0,005 - 0,035 |
|
Омыленный талловый пек |
отп |
0,005 - 0,035 |
|
Смола древесная омыленная |
СДо |
0,005 - 0,035 |
|
Вспомогательный препарат |
оп |
0,005 - 0,035 |
|
Сульфонол |
с |
0,005 - 0,035 |
2.Пластифицирующие |
Щелочной сток производства капролактама |
щспк |
0,1 - 0,5 |
воздухововлекающие |
Модифицированный щелочной сток производства капролактама |
ЩСПК-м |
0,05 - 0,2 |
|
Черный сульфатный щелок |
ЧСЩ |
0,05-0,2 |
|
Модифицированная синтетическая поверхностно-активная |
СПД-м |
0,05 - 0,02 |
|
Смола омыленная водорастворимая |
ВЛХК |
|
|
Понизитель вязкости фенольный лесохимический |
ПФЛХ |
0,05 - 0,2 |
|
Лесохимическая |
ЛХД |
0,05 - 0,2 |
|
Нейтрализованный черный контакт |
НЧК |
0,1ѕ0,2 |
|
Контакт черный нейтрализованный рафинированный |
КЧНР |
0,1ѕ0,2 |
3. Газообразующие |
Пудра алюминиевая |
ПАК |
0,01 - 0,03 |
4. Гидрофобизирующие |
Полифенилэтоксилоксаны** |
фэс-50; ФЭС-66 |
1 - 2;
1 - 2 |
5. Гидрофобизирующие |
Этилсиликонат натрия |
гкж-10 |
0,05ѕ0,2 |
воздуховов- |
Метилсиликонат натрия |
ГКЖ-11 |
0,05 - 0,2 |
лекающие |
Алюмометилсиликонат натрия |
АМСР |
0,05 - 0,2 |
|
Мылонафт |
М1 |
0,05ѕ0,2 |
6. Гидрофобизирующие |
Полигидросилоксан 136-41 |
ГКЖ-94 |
0,05 - 0,1 |
газовыделяющие |
Полигидросилоксан 136-157м |
ГКЖ-94М |
0,03 - 0,08 |
|
Этилгидридсесквиоксан |
ПГЭН |
0,05 - 0,1 |
7. Уплотняющие |
Диэтиленгликолевая смола |
ДЭГ-1 |
1ѕ1,5 |
|
Триэтиленгликолевая смола |
ТЭГ-1 |
1ѕ1,5 |
|
Полиаминная смола |
С-89 |
0,6 - 1,5 |
|
Битумная эмульсия (эмульбит) |
БЭ |
5 - 10 |
|
Сульфат алюминия |
СА |
1,5ѕ3 |
|
Сульфат железа |
СЖ |
1,5ѕ3 |
|
Нитрат железа |
НЖ |
1,5 - 3 |
|
Нитрат кальция |
НК |
1,5 - 3 |
8. Суперпластификаторы |
Разжижитель С-3 |
С-3 |
0,3 - 1 |
|
10-03 |
10-03 |
0,3ѕ1 |
|
Дофен |
Дф |
0,5 - 1 |
|
Меламинформальдегидная смола МФ-АР |
МФ-АР |
0,3 - 1 |
|
НКНС 40-03 |
40-03 |
0,2ѕ1 |
|
Разжижитель СМФ |
СМФ |
0,3ѕ1 |
9. Пластифицирующие |
Лигносульфонат технический |
ЛСТ |
0,15ѕ0,5 |
|
Модифицированные лигносульфонаты*** |
|
|
|
Мелассная упаренная последрожжевая барда |
УПБ |
0,15 - 0,3 |
|
Водорастворимый препарат ВРП-1 |
ВРП-1 |
0,005 - 0,03 |
|
Водорастворимый препарат С-1 |
С-1 |
0,005 - 0,03 |
|
Плав дикарбоновых кислот |
ПДК |
0,4ѕ1 |
|
Аплассан |
АПЛ |
0,4 - 1 |
10. Стабилизирующие |
Полиэтиленоксид, полиоксиэтилен |
ПОЭ |
0,02ѕ0,2 |
11. Ингибиторы |
Нитрит натрия |
НН |
2 - 3 |
коррозии стали |
Тетраборат натрия |
ТБН |
0,5ѕ1,5 |
|
Бихромат натрия |
БХН |
0,5 |
|
Бихромат калия |
БХК |
0,5 |
|
Нитрит-нитрат кальция |
ННК |
2 - 3 |
|
Катапин-ингибитор |
КН-1 |
0,025ѕ0,15 |
* Дозировки добавок указаны в % массы цемента в пересчете на сухое вещество добавки или 100 %-ный продукт и зависят от вида применяемого цемента, состава бетона, технологии изготовления изделий и конструкций и условий их эксплуатации.
** Полифенилэтоксилоксаны могут быть использованы только в бетонах нормального твердения.
*** Модифицированные лигносульфонаты (ЛСТМ-2, ХДСК-1, ХДСК-3, НИЛ-21, МЛС, ОКЗИЛ, МТС-1) повышают стойкость бетонов за счет водоредуцирующего действия (В/Ц может быть снижено на 10-15 %). |
Таблица 2
Допустимые области применения некоторых химических добавок в зависимости от их коррозионного воздействия на арматуру
Изделия и |
Область применения добавок* |
конструкции, условия их эксплуатации |
ХЖ, ХК, ХН |
ННХК |
УПБ |
НК,ННК |
НЖ |
СН, ТНФ |
БХН, БХК |
НН, НН1 |
СА, СЖ |
ТБН |
1. Предварительно напряженные изделия и конструкции |
- |
- |
- |
+ |
+ |
+ |
+ |
+ |
+ |
+ |
2. То же, армированные сталью классов aт-v, aт-vi, A-V, A-VI |
ѕ |
ѕ |
ѕ |
ѕ |
ѕ |
+ |
+ |
+ |
+ |
+ |
3. Железобетонные изделия и конструкции с ненапряженной рабочей арматурой диаметром 5 мм и менее |
ѕ |
+ |
+ |
+ |
+ |
+ |
+ |
+ |
+ |
+ |
4. Железобетонные изделия и конструкции, имеющие выпуски арматуры или закладные детали; |
|
|
|
|
|
|
|
|
|
|
а) без специальной защиты стали |
ѕ |
ѕ |
+ |
+ |
+ |
+ |
+ |
+ |
+ |
+ |
б) с цинковыми покрытиями по стали |
- |
- |
+ |
ѕ |
ѕ |
- |
ѕ |
+ |
+ |
+ |
в) с алюминиевым покрытием по стали |
ѕ |
+ |
+ |
+ |
+ |
ѕ |
ѕ |
ѕ |
+ |
+ |
5. Железобетонные изделия и конструкции, предназначенные для эксплуатации: |
|
|
|
|
|
|
|
|
|
|
а) в агрессивных газовых средах |
ѕ |
+ |
+ |
+ |
+ |
+ |
+ |
+ |
+ |
+ |
б) в зоне переменного уровня воды и в зонах действия блуждающих постоянных токов от посторонних источников |
ѕ |
ѕ |
ѕ |
+ |
+ |
+ |
+ |
+ |
+ |
+ |
в) в агрессивных сульфатных водах и в растворах солей и едких щелочей при наличии испаряющих поверхностей |
ѕ |
ѕ |
+ |
ѕ |
ѕ |
+ |
+ |
+ |
+ |
+ |
6. Железобетонные изделия и конструкции для электрифицированного транспорта и промышленных предприятий, потребляющих постоянный электрический ток |
ѕ |
ѕ |
ѕ |
ѕ |
ѕ |
ѕ |
ѕ |
ѕ |
ѕ |
ѕ |
* Условные обозначения добавок приведены в табл. 1 прил. 5. Условные обозначения добавок, не вошедших в табл. 1:
ХК - хлорид кальция, ХН - хлорид натрия, СН ѕ сульфат натрия, ННХК - нитрит-нитрат-хлорид кальция, ТНФ - тринатрийфосфат, HH1 - нитрат натрия, НН - нитрит натрия.
Примечания: 1. Возможность применения добавок по пп. 1 - 4 должна уточняться с учетом требований п. 5, а по п. 3 - требований п. 4.
2. Требования пп. 4 и 5в распространяются и на бетонные изделия и конструкции.
3. По п. 5а в средах, содержащих хлор или хлористый водород, добавки НН и ННК разрешается применять без ограничений, остальные - после проведения соответствующего эксперимента.
4. Добавку НЖ запрещается применять в бетонах, подвергающихся тепловой обработке или периодическому нагреванию выше 70 °С при эксплуатации. |
Таблица 3
ОРИЕНТИРОВОЧНЫЕ СВОЙСТВА БЕТОННЫХ СМЕСЕЙ И БЕТОНОВ С ХИМИЧЕСКИМИ ДОБАВКАМИ
|
Улучшение характеристик бетонных смесей и бетонов |
|
при постоянном В/Ц |
при равной подвижности смеси |
Добавки |
подвижности смеси от 2 - 4 см до |
морозостойкости, на число марок |
водонепроницаемости, на число марок |
коррозионной стойкости, %* |
морозостойкости, на число марок |
водонепроницаемости, на число марок |
коррозионной стойкости, %* |
1 |
2 |
3 |
4 |
5 |
6 |
7 |
8 |
снв, ктп, отп, сдо, оп, с |
- |
1-2 |
1 |
150-200 |
3-4 |
1-2 |
150-200 |
щспк, чсщ |
8-10 |
1 |
- |
150 |
2 |
1-2 |
150-200 |
ЩСПК-м, СПД-м |
8-10 |
1-2 |
- |
150 |
2-3 |
1-2 |
150-200 |
нчк, КЧНР, м, гкж-10, ГКЖ-11, АМСР |
6-8 |
1ѕ2 |
- |
150 |
2-3 |
1ѕ2 |
150-200 |
ФЭС-50, ФЭС-66 |
- |
1-2 |
|
200-300** |
1ѕ2 |
ѕ |
200-300** |
ГКЖ-94, ГКЖ-94М, ПГЭН |
4-6 |
3-4 |
- |
150-200 |
4-5 |
1-2 |
150-250 |
ДЭГ-1, ТЭГ-1, С-89, БЭ |
6-8 |
- |
2-3 |
200-300 |
1-2 |
3-4 |
300-400 |
СА, СЖ, ХЖ, НЖ, НК |
- |
ѕ |
2-3 |
200-300 |
ѕ |
2-3 |
200-300 |
С-3, 10-03, ДФ, МФ-АР, 40-03, СМФ |
20-22 |
- |
- |
- |
1 |
3-4 |
150-200 |
ЛСТ, УПБ, ВРП-1, С-1, ПДК, АПЛ |
8-12 |
- |
- |
- |
1 |
2 |
150-200 |
* Не распространяется на коррозионную стойкость бетона при коррозии II вида. За 100 % принимается коррозионная стойкость бетона исходного состава без добавок.
** Эффективность добавок ФЭС в максимальной степени проявляется в условиях капиллярного подсоса растворов солей и испарения. |
ПРИЛОЖЕНИЕ 6
Ускоренное определение способности пористого заполнителя связывать гидроксид кальция
1. Определение активности пористого заполнителя заключается в оценке его способности поглощать гидроксид кальция из его насыщенного раствора.
2. Применяемая аппаратура, и реактивы: гидроксид кальция, насыщенный раствор; соляная кислота, концентрации 0,05 мольЧл 1; индикатор метиловый оранжевый; штатив с бюреткой на 50 мл; сосуд из фторопласта или другого инертного к щелочам материала; стакан или стеклянная коническая колба для титрования; пипетка для отбора проб.
Приготовление насыщенного раствора гидроксида кальция
В бутыль вместимостью 20-25 л помещают 50 г гидроксида кальция, наливают дистиллированной воды (15 л) и плотно закрывают резиновой пробкой, в которую вставлена трубка с натронной известью. Раствор взбалтывают 2-3 раза в сут.
Через 3-4 сут бутыль вскрывают, отфильтровывают небольшое количество раствора, отбирают пипеткой 50 мл в коническую колбу и титруют раствором соляной кислоты.
Если результат титрования покажет, что раствор имеет концентрацию не ниже 1,15 СаО на 1 л, то приступают к его фильтрованию; в противном случае подвергают дальнейшему насыщению.
3. Подготовка испытуемой пробы и проведение испытания.
Определяют активность любой требуемой фракции пористого заполнителя. Отбирают среднюю пробу испытуемого материала в количестве 100 г и высушивают до постоянной массы. От подготовленной пробы берут навеску массой 1 г, взвешивают на аналитических весах с точностью до 4-го знака. Навеску помещают в плотно закрывающийся сосуд из фторопласта или другого стойкого к щелочам материала и заливают 100 мл насыщенного раствора гидроксида кальция (соотношение навески и раствора может быть больше 1:100 для высокоактивных материалов). Сосуд закрывают пробкой и выдерживают при температуре 85 - 90 °С не менее 8 ч. После чего сосуд вынимают, охлаждают 15 мин под струей воды при температуре 16 - 20 °С, отбирают 50 мл раствора пипеткой, добавляют 2 - 3 капли раствора метилового оранжевого и титруют раствором соляной кислоты до появления розовой окраски.
4. Обработка результатов.
Количество СаО в мг, поглощенное 1 г заполнителя, определяют по формуле СаО = (vо - v)2 ТЧ103,
где vо - количество раствора соляной кислоты, пошедшего на титрование 50 мл насыщенного раствора гидроксида кальция, мл; v - количество раствора соляной кислоты, пошедшее на титрование 50 мл анализируемого раствора; Т - титр раствора соляной кислоты по СаО, равный 0,0014 г/мл.
ПРИЛОЖЕНИЕ 7
Выбор типа изоляции
|
Изоляция |
Требования к изоляции |
торкрет-штукатурка |
битумная** |
битумно-полимерная |
асфальтовая |
Полимерная |
|
на цементе |
с полимерными добавками **** |
окрасочная |
пропиточная |
оклеечная |
окрасочная |
пропиточная |
оклеечная |
холодная |
горячая |
горячая литая |
окрасочная |
оклеечная |
1 |
2 |
3 |
4 |
5 |
6 |
7 |
8 |
9 |
10 |
11 |
12 |
13 |
14 |
По величине напора воды: |
|
|
|
|
|
|
|
|
|
|
|
|
|
противокапиллярная |
- |
- |
++ |
- |
- |
++ |
- |
- |
+ |
= |
- |
- |
- |
нормальная (величина напора до 10 м) |
+ |
+ |
+* |
+ |
+ |
+ |
+ |
+ |
+ |
+ |
= |
+** |
= |
усиленная (величина напора более 10 м) |
+ |
++ |
- |
+ |
+ |
- |
+ |
+ |
+ |
+ |
+ |
+ |
+ |
при работе на отрыв |
+ |
++ |
- |
+ |
о, анк. |
- |
+ |
о, анк. |
++ |
- |
о, анк. |
++ |
++ |
По химической агрессивности воды-среды: |
|
|
|
|
|
|
|
|
|
|
|
|
|
выщелачивающая |
- |
+ |
+ |
+ |
+ |
+ |
+ |
+ |
+ |
+ |
- |
= |
= |
общекислотная |
- |
- |
+ |
+ |
+ |
+ |
+ |
+ |
|
++C |
++ |
++ |
++ |
углекислотная |
+ |
+ |
+ |
+ |
+ |
+ |
+ |
+ |
о, с |
+ |
+ |
+ |
+ |
магнезиальная |
- |
+ |
+ |
+ |
+ |
+ |
+ |
+ |
0, с |
+ |
+ |
+ |
+ |
сульфатная |
- |
+ |
+ |
+ |
+ |
+ |
+ |
+ |
0, с |
+ |
+ |
+ |
+ |
нефтехимическая |
о, окр. |
+ |
- |
- |
- |
- |
- |
- |
- |
- |
- |
++ |
++ |
электрохимическая |
- |
- |
0, окр. |
+ |
+ |
+ |
+ |
+ |
- |
+ |
+ |
+ |
+ |
По механической прочности |
+ |
+ |
+ |
+ |
+ |
+ |
+ |
+ |
+ |
- |
- |
+ |
- |
По трещиностойкости: |
|
|
|
|
|
|
|
|
|
|
|
|
|
без трещин |
+ |
+ |
+ |
+ |
+ |
+ |
+ |
+ |
++ |
++ |
- |
+ |
- |
трещины до 0,3 мм |
0, арм. |
+ |
0, арм. |
- |
+ |
0, арм. |
- |
++ |
+ |
+ |
- |
0, арм. |
- |
По внешним воздействиям: |
|
|
|
|
|
|
|
|
|
|
|
|
|
надземная зона |
+ |
+ |
0, с |
+ |
0, защ. |
0, с |
+ |
+ |
+ |
- |
- |
0, с |
+ |
подземная зона |
+ |
+ |
+ |
+ |
+ |
+ |
+ |
+ |
++ |
+ |
+ |
+ |
+ |
По условиям производства работ: |
|
|
|
|
|
|
|
|
|
|
|
|
|
строительная площадка |
+ |
+ |
+ |
+ |
+ |
+ |
+ |
+ |
+ |
+ |
+ |
+ |
+ |
зимние условия |
0, с |
0, с |
0, с |
+ |
0, с |
0, с |
0, с |
0, с |
0, с |
0, с |
++ |
|
0, с |
* Покрытие выдерживает напор до 3 м.
** Покрытие выдерживает напор до 5 м.
*** Кислоты, в которых битумная гидроизоляция нестойка, приведены в прил. 8.
Условные обозначения: ++ - имеет безусловное преимущество; + - рекомендуется; - - не рекомендуется; = - возможно при экономическом обосновании; 0 - требуются дополнительные мероприятия; с - со специальным подбором состава; защ. - со специальным защитным ограждением; окр. - с дополнительной окраской поверхности; анк. - с анкеровкой; арм. - с армированием.
**** По Рекомендациям по составу и области применения коррозионно-стойкого торкрета с полимерными добавками. - Ростов-на-Дону, ПСНИИпроект, 1981. |
ПРИЛОЖЕНИЕ 8
Химическая стойкость материалов в агрессивных средах
Таблица 1
Битумы и гудроны при температуре 25 °С в различных средах
Среда, где состояние материала характеризуется как устойчивое |
Среда, где состояние материала характеризуется как неустойчивое |
Вода |
ѕ |
Кислоты: серная (55 %-ная), азотная (10 %-ная), соляная (30 %-ная), фосфорная (85 %-ная), уксусная (10 %-ная), Н2SО3 (любой концентрации), гуминовая, молочная, борная, масляная, бензойная, лимонная (10 %-ная), кремнефтористая (40 %-ная), щавелевая (20 %-ная), стеариновая |
Кислоты: уксусная (>10 %), хлоруксусная (10 %-ная), хромовая (>10 %), жирные кислоты, муравьиная (90 %-ная), азотная (>10 %), олеиновая (100 %-ная), пикриновая (100 %-ная), серная (>70 %), олеум |
Соли: карбонаты, нитраты, хлориды, сульфаты, фториды, электролиты, моющая сода, нашатырь, селитра, сульфитный щелок, квасцы, бикарбонаты (10 %), фосфаты (10 %) |
Растворители: ацетон (100 %-ный), анилин, хлороформ, фенол, этиловый эфир уксусной кислоты, газолин, бензол, жидкие углеводороды, сероуглерод |
Разнообразные органические материалы: пахтаны, яблочный сок, кукурузная патока, молочная сыворотка, глюкоза, молоко, силос, спирты, формальдегид (37 %-ный), жидкие отходы бумажной промышленности, удобрения, отходы текстильной и пищевой промышленности, пивоваренных заводов, сыворотки, кожевенных предприятий и др. |
Сильные окислители:
Н2CrО4 и др. |
Разнообразные неорганические материалы: вода, загрязненная примесями неорганических веществ, отходы фотографические, металлизационные, металлургической промышленности; серная кислота для травления |
Минеральные масла |
Щелочи: гидрооксид аммония (28 %-пая), гидросксид кальция (насыщенная), потат, гидрооксид натрия (25 %-ная)
Газы: увлажненный сернистый ангидрид, сероводород |
ѕ |
Таблица 2
Химическая стойкость антикоррозионных материалов в некоторых агрессивных органических средах
Среда |
Облицовочных материалы |
Мастики, замазки, лакокрасочные материалы на основе |
|
кислотостойкая керамика |
шлакоситалл |
керамическая плитка |
каменное литье |
силиката натрия |
перхлорвиниловой смолы |
фенолформальдегидной смолы |
полиэфирной смолы (насыщенной) |
Октан* |
|
|
|
|
++ |
++ |
++ |
++ |
Декан* |
|
|
|
|
++ |
++ |
++ |
++ |
Бензол |
++ |
++ |
++ |
++ |
++ |
- |
++ |
- |
Толуол |
++ |
++ |
++ |
++ |
++ |
- |
++ |
++ |
Ксилол |
++ |
++ |
++ |
++ |
++ |
- |
++ |
+ |
Ацетон |
++ |
++ |
++ |
++ |
++ |
- |
+ |
- |
Этанол (водный раствор 30 %) |
++ |
++ |
++ |
++ |
+ |
+ |
++ |
+ |
Гептанол |
++ |
++ |
++ |
++ |
++ |
+ |
++ |
++ |
Деканол* |
|
|
|
|
++ |
++ |
++ |
++ |
Глицерин* |
|
|
|
|
+ |
++ |
++ |
++ |
Диметилформамид (водный раствор 40%) |
++ |
++ |
++ |
++ |
+ |
ѕ |
++ |
ѕ |
Фенол |
++ |
++ |
++ |
++ |
++ |
++ |
++ |
++ |
Формалин |
++ |
++ |
++ |
++ |
++ |
++ |
++ |
++ |
Тетрагидрофуран* - бутиролактон |
|
|
|
|
++ |
ѕ |
++ |
ѕ |
Уксусная кислота (водный раствор, %): |
|
|
|
|
|
|
|
|
10 |
++ |
++ |
- |
++ |
++ |
++ |
++ |
- |
40 |
++ |
++ |
- |
++ |
++ |
+ |
++ |
- |
60 |
++ |
++ |
- |
++ |
++ |
+ |
++ |
- |
92 |
++ |
++ |
- |
++ |
++ |
- |
++ |
- |
Муравьиная кислота (водный раствор, %): |
|
|
|
|
|
|
|
|
10 |
++ |
++ |
- |
++ |
++ |
+ |
++ |
++ |
20 |
++ |
++ |
- |
++ |
++ |
- |
++ |
- |
40 |
++ |
++ |
- |
++ |
++ |
- |
++ |
- |
80 |
++ |
++ |
ѕ |
++ |
++ |
ѕ |
+ |
ѕ |
Бензолсульфокислота (водный раствор, %): |
|
|
|
|
|
|
|
|
15 |
++ |
++ |
+ |
+ |
++ |
++ |
++ |
|
50* |
|
|
|
|
++ |
++ |
++ |
|
80* |
|
|
|
|
++ |
++ |
++ |
|
Каприновая кислота |
++ |
++ |
+ |
+ |
++ |
+ |
++ |
++ |
Продолжение табл. 2
|
Мастики, замазки, лакокрасочные материалы на основе |
Оклеечные гидроизоляционные материалы |
Среда |
полиуретановой смолы |
битума |
хлорсульфированного полиэтилена |
эпоксидной смолы |
рубероид, бризол, изол |
полиизобутилен |
полиэтилен |
Октан* |
++ |
ѕ |
++ |
++ |
|
|
|
Декан* |
++ |
- |
++ |
++ |
|
|
|
Бензол |
++ |
- |
+ |
++ |
ѕ |
++ |
++ |
Толуол |
+ |
- |
- |
++ |
- |
++ |
++ |
Ксилол |
+ |
- |
- |
++ |
- |
++ |
++ |
Ацетон |
- |
- |
- |
+ |
- |
++ |
++ |
Этанол (водный раствор 30 %) |
++ |
+ |
++ |
++ |
+ |
++ |
++ |
Гептанол |
++ |
- |
++ |
++ |
+ |
++ |
++ |
Деканол* |
++ |
|
++ |
++ |
|
|
|
Глицерин* |
++ |
+ |
++ |
++ |
|
|
|
Диметилформамид (водный раствор 40%) |
ѕ |
++ |
++ |
++ |
ѕ |
++ |
++ |
Фенол |
++ |
++ |
++ |
ѕ |
++ |
++ |
++ |
Формалин |
++ |
++ |
++ |
++ |
++ |
++ |
++ |
Тетрагидрофуран* - бутиролактон |
ѕ |
ѕ |
ѕ |
+ |
|
|
|
Уксусная кислота (водный раствор, %): |
|
|
|
|
|
|
|
10 |
++ |
++ |
++ |
++ |
++ |
++ |
++ |
40 |
- |
++ |
+ |
- |
+ |
++ |
++ |
60 |
- |
++ |
+ |
- |
+ |
++ |
++ |
92 |
- |
- |
- |
- |
- |
++ |
++ |
Муравьиная кислота (водный раствор, %): |
|
|
|
|
|
|
|
10 |
++ |
++ |
++ |
++ |
++ |
++ |
++ |
20 |
++ |
++ |
+ |
- |
+ |
++ |
++ |
40 |
- |
++ |
+ |
- |
+ |
++ |
++ |
80 |
|
+ |
ѕ |
ѕ |
+ |
++ |
++ |
Бензолсульфокислота (водный раствор, %): |
|
|
|
|
|
|
|
15 |
++ |
++ |
- |
++ |
|
|
|
50* |
+ |
+ |
- |
++ |
|
|
|
80* |
- |
- |
- |
++ |
|
|
|
Каприновая кислота |
++ |
- |
+ |
++ |
- |
++ |
++ |
* Химическую стойкость антикоррозионных материалов, не указанную в настоящей таблице, следует уточнять по литературным данным или экспериментальным путем.
Примечание. Знаком (-) показаны антикоррозионные материалы нестойкие; (+) - относительно стойкие; (++) - стойкие. |
ПРИЛОЖЕНИЕ 9
Химическая стойкость материалов для покрытия полов
|
|
Химическая стойкость материалов для покрытий полов на основе |
Среда |
Концентрация среды*, % |
кислотоупорной керамики |
жидкого стекла |
битума и песка |
термопластов** |
цемента*** |
Щелочи: |
|
|
|
|
|
|
едкий натр |
Св. 10 |
± |
- |
± |
++ |
± |
|
Св. 5 до 10 |
+ |
- |
+ |
++ |
+ |
|
Св. 1 до 5 |
++ |
- |
+ |
++ |
+ |
|
До 1 |
++ |
- |
++ |
++ |
++ |
Основания: |
|
|
|
|
|
|
известь, сода, основные соли |
Не ограничивается |
++ |
ѕ |
++ |
++ |
± |
Кислоты: |
|
|
|
|
|
|
минеральные |
Св. 5 |
++ |
++ |
± |
++ |
- |
не окисляющие |
Св. 1 до 5 |
++ |
++ |
± |
++ |
± |
|
До 1 |
++ |
± |
++ |
++ |
+ |
органические |
Св. 5 |
++ |
++ |
±**** |
++ |
± |
|
Св. 1 до 5 |
++ |
++ |
+ |
++ |
+ |
|
До 1 |
++ |
+ |
++ |
++ |
+ |
Кислоты |
Св. 5 |
++ |
++ |
ѕ**** |
± |
- |
окисляющие |
Св. 1 до 5 |
++ |
++ |
± |
+ |
- |
|
До 1 |
++ |
± |
+ |
++ |
± |
Растворы сахара, |
Не ограни- |
++ |
++ |
± |
++ |
- |
патоки |
чивается |
++ |
++ |
- |
++ |
- |
Масла, жиры |
To же |
|
|
|
|
|
Растворители: |
|
|
|
|
|
|
ацетон, бензин и др. |
» |
++ |
++ |
ѕ |
++ |
+ |
* Концентрация агрессивных растворов не должна превышать 20 %. При больших концентрациях агрессивных растворов возможность применения материалов следует определять по соответствующим ГОСТам.
** К термопластам относятся полиэтилен, поливинилхлорид, фторопласт, полиизобутилен, полипропилен и др.
*** Химическая стойкость покрытия полов из цементного бетона может быть повышена введением полимерных добавок или поверхностной пропиткой.
**** Материалы на основе битумов стойки в 10 %-ной азотной, хромовой и уксусной кислотах.
Примечания: 1. Знаком минус (-) показаны материалы нестойкие, (±) - малостойкие, (+) - относительно стойкие, (++) - стойкие.
2. Малостойкие и относительно стойкие материалы могут быть применены при наличии технико-экономического обоснования. |
ПРИЛОЖЕНИЕ 10
Требования к источникам блуждающих токов отделений электролиза
Общие указания
1. Выпрямители преобразовательных подстанций электролизных цехов на стороне постоянного тока должны быть надежно изолированы от земли и строительных конструкций. Сопротивление изоляции обеих шин выпрямителя относительно земли при отключенной электролизной установке должно быть не ниже 0,5 МОм.
2. При многорядовом расположении электролизных установок подключение их к выпрямителям рекомендуется выполнять так, чтобы соседние электролизные установки были обращены друг к другу участками одинаковой полярности.
3. Шины, технологические трубопроводы, желоба, как металлические, так и выполненные из неэлектропроводных материалов, должны быть изолированы от строительных конструкций воздушными зазорами не менее 50 мм, а от заземленного оборудования (баков, насосов и т. п.) и стоек под оборудование, не защищенных специальной оклеечной изоляцией, - зазорами не менее 200 мм.
4. Все проемы в местах пересечения шин и металлических трубопроводов с железобетонными конструкциями оборудуются гильзами и вставками из электроизоляционных материалов.
5. Для крепления трубопроводов и шин рекомендуется применять кронштейны из электроизоляционных материалов (например, армированного винипласта) (рис. 1) или металлические кронштейны и подвески с изоляцией в двух точках (рис. 2). Крепление кронштейнов к железобетонным конструкциям следует осуществлять с помощью обжимных хомутов, накладываемых на бетонную поверхность конструкции.
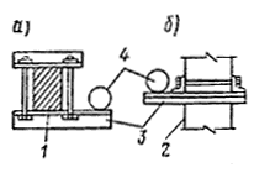
Рис. 1. Примеры выполнения держателей из электроизоляционных материалов для крепления трубопроводов
а - к балке; б - к колонне; 1 - железобетонная балка; 2 - железобетонная колонна; 3 - держатель из электроизоляционных материалов; 4 - трубопровод
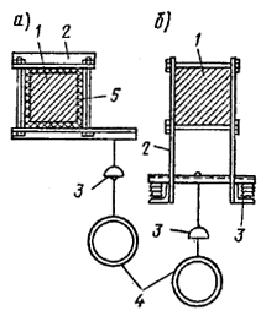
Рис. 2. Примеры выполнения металлических держателей для крепления трубопроводов
а - с электроизоляционной вставкой в подвеске и в местах крепления хомута к железобетонной конструкции; б - с двумя электроизоляционными вставками в подвеске; 1 - железобетонная конструкция; 2 - металлический держатель; 3 - изолятор; 4 - трубопровод; 5 - изоляционная прокладка
Крепления и подвески, пропускаемые через железобетонные конструкции, не рекомендуются. При вынужденном использовании таких креплений и подвесок места контакта с железобетонными конструкциями должны оборудоваться электроизоляционными вставками (рис. 3) или закладные детали креплений должны устанавливаться на полимерном клее.

Рис. 3. Пример подвесок типа шпильки для крепления технологических трубопроводов
а - одиночного; б - нескольких; 1 - железобетонная конструкция; 2 а, б, в - конструкция пола (а - бетонное основание пола; б - химически стойкая гидроизоляция, в - покрытие пола); 3 - диэлектрическая гильза; 4 - металлическая тяга; 5 - изолятор; 6 - изоляционная прокладка; 7 - трубопровод; 8 - поддерживающая конструкция
Примечание. При выборе материала для кронштейнов следует учитывать теплостойкость материала.
6. Железобетонные конструкции не должны иметь контакта с подземными шпунтами или подземными металлическими контурами (грозозащитными, дренажными и др.).
Отделения электролиза водных растворов
7. Для изоляции электролизеров, шин, трубопроводов и другого технологического оборудования рекомендуется применять подвесные и опорные изоляторы зонтичного типа для наружных установок на соответствующие механические нагрузки и напряжение 3 - 6 кВ.
8. Рекомендуется технологические трубопроводы крепить через изоляционные подвески к элементам электролизных ванн, избегая креплений к железобетонным конструкциям (рис. 4).
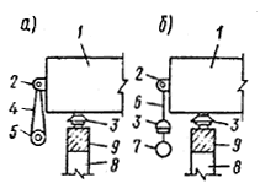
Рис. 4. Схема подвески технологических трубопроводов к конструкциям электролизных ванн
а - подвеска и трубопровод из электроизоляционного материала; б - металлические подвеска и трубопровод; 1 -электролизная ванна; 2 - подъемная петля; 3 - изолятор; 4 - подвеска из пластиката; 5 - винипластовый трубопровод; 6 - металлическая подвеска; 7 - металлический трубопровод; 8 - железобетонная колонна; 9 - железобетонная балка
9. Трубопроводы и желоба, по которым транспортируют электролит и продукты электролиза, должны, как правило, выполняться из неэлектропроводных материалов (фторопласт, стеклопластики, фаолит и др.).
10. Металлические трубопроводы, соединяемые с электролизерами, могут применяться только при соблюдении следующих условий:
а) внутренняя поверхность металлических труб должна быть гуммирована или защищена другими электроизоляционными и химически стойкими покрытиями; монтаж трубопроводов осуществляется с электроизоляцией стыков; при применении титановых или других металлических трубопроводов, обладающих высокой коррозионной стойкостью и используемых без защиты внутренней поверхности, уменьшение блуждающих токов должно быть выполнено по специальному проекту;
б) соединение с электролизерами должно осуществляться трубами и шлангами из неэлектропроводных материалов длиной не менее 3 м; уменьшение длины вставок до 1 м возможно на газопроводах при условии выполнения вставок из фторопласта-4;
в) соединение рядовых трубопроводов (коллекторов) со сборным трубопроводом должно производиться трубами из неэлектропроводных материалов длиной не менее 6 м во всех случаях, кроме газопроводов, соединение которых с электролизерами выполняется с помощью вставок из фторопласта-4;
г) на всех металлических трубопроводах в местах перехода из грунта в электролизное отделение должны устанавливаться электроизолирующие вставки для разрыва цепи тока по трубопроводу.
11. Для разрыва струи поступающего и вытекающего электролита рекомендуется снабжать электролизеры капельницами и другими устройствами.
12. Ввод электролита в коллекторы и вывод продуктов электролиза из коллекторов электролизной установки, а также присоединение технологического оборудования к электролизной установке необходимо осуществлять в местах с наименьшим потенциалом относительно земли ближе к нейтральной точке (рис. 5, 6).
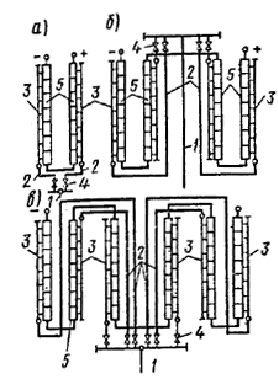
Рис. 5. Схема ввода электролитов в коллекторы электролизной установки, обладающая минимальными токами утечки
а, б, в - схемы с двумя, четырьмя и шестью рядами электролизеров соответственно; 1 - труба ввода электролита в цех; 2 - труба ввода электролита в коллектор; 3 - рядовой коллектор электролита; 4 - вентиль; 5 - электролизеры
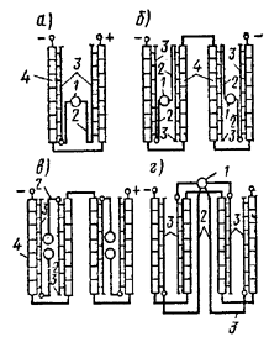
Рис. 6. Схемы присоединения технологического оборудования к электролизной установке с уменьшенными токами утечки
а - схема с двумя рядами электролизеров и общим сборным баком; б - схема с четырьмя рядами электролизеров и двумя сборными баками; в, г - схема с четырьмя рядами электролизеров и одним сборным баком; 1 - сборный бак электролита; 2 - отводящий трубопровод; 3 - рядовой коллектор с электролитом; 4 - электролизеры
13. Технологическое оборудование необходимо располагать в цехе и подключать к электролизной установке симметрично относительно середины электролизной установки.
14. Каждый ряд электролизеров должен иметь индивидуальные коллекторы или желоба, транспортирующие входящие электролиты и продукты электролиза.
15. Катодная, дренажная и протекторная защита оборудования электролизных установок может быть применена только после специальных проектных разработок и экспериментальных исследований, подтверждающих, что применение защиты уменьшает ток утечки через защищаемый участок и не приводит к резкому увеличению тока утечки на незащищенных участках.
Отделения электролиза расплавов
Напольные металлические решетки, находящиеся под потенциалом катода электролизера, должны быть электроизолированы от несущих строительных конструкций.
В отделениях электролиза расплавов солей аммония допускается использовать в качестве электроизоляционных материалов: ацеид, асбокартон, асбест (в сухом состоянии).
ПРИЛОЖЕНИЕ 11
Схема электрозащиты блочной железобетонной конструкции
Схему электродренажной защиты (рис. 1, а) рекомендуется предусматривать для железобетонных конструкций, расположенных в знакопеременных зонах потенциалов электрифицированных рельсовых путей, в которых преобладают по величине и времени катодные значения потенциалов более 1 В.
Схему катодной защиты (рис. 1, б) рекомендуется предусматривать для железобетонных конструкций, расположенных в анодных зонах потенциалов электрифицированных рельсовых путей. При этом в случае необходимости глухого соединения блочных конструкций между собой соединения должны выполняться в соответствии с рис. 2.
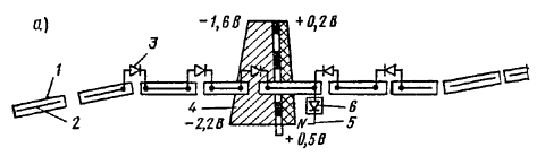
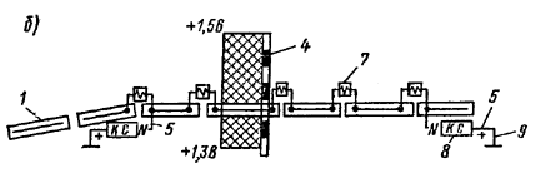
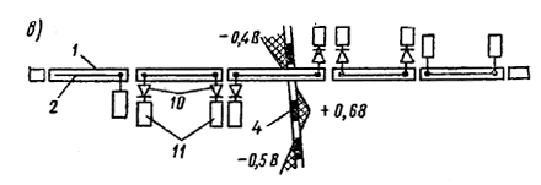
Рис. 1. Схемы защиты блочной железобетонной конструкции
а - электродренажная защита; б - катодная защита; в - протекторная защита; 1 - отдельный железобетонный блок; 2 - арматурный каркас блока; 3 ѕ регулируемая вентильная перемычка; 4 - рельсовый путь электрифицированной железной дороги и потенциальная диаграмма; 5 - дренажный кабель; 6 - устройство электрического дренажа; 7 - регулируемая перемычка; 8 - источник постоянного тока (катодная станция); 9 - анодное заземление; 10 - диод; 11 - протектор
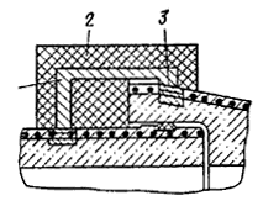
рис. 2. Общий вид перемычки между арматурой смежных секций труб
1 - стальная полоса 10ґ60 мм; 2 - битум марки IV; 3 - закладные части, установленные на арматурном каркасе
Схему протекторной защиты (см. рис. 1) рекомендуется предусматривать для железобетонных конструкций, расположенных в знакопеременных зонах потенциалов при значениях потенциалов «рельс-земля» в пределах ±1 В.
ПРИЛОЖЕНИЕ 12
Усредненные исходные параметры для предварительной оценки экономической эффективности антикоррозионной защиты железобетонных конструкций
Таблица 1
Усредненные показатели стоимости конструкций, изделий, материалов и удельных капитальных вложений в организацию их производства
Конструкции, изделия и материалы |
Единица измерения |
Стоимость единицы измерения «в деле», руб. |
Удельные капитальные вложения, руб. |
1 |
2 |
3 |
4 |
1. Сборные железобетонные конструкции и изделия для промышленного и сельскохозяйственного строительства |
|
|
|
Элементы фундаментов |
м3 |
58 |
53 |
Колонны, стойки |
» |
125 |
78 |
Балки, прогоны, ригели |
м3 |
106 |
70 |
Фермы |
» |
163 |
137 |
Шиты покрытий и перекрытий |
» |
93 |
81 |
Стеновые панели |
» |
75 |
67 |
2. Материалы, используемые для сборных и монолитных железобетонных конструкций |
|
|
|
Арматурная сталь для сборных конструкций |
т |
177 |
450 |
Арматурная сталь для монолитных конструкций |
» |
166 |
430 |
Бетон товарный |
м3 |
24 |
5 |
Раствор товарный |
» |
20 |
5 |
3. Материалы для антикоррозионной защиты |
|
|
|
Бетон защитного слоя арматуры |
м3 |
55 |
50 |
Лаки химстойкие нетрещиностойкие (ХС, ХВ) |
т |
600 |
715 |
Лаки химстойкие трещиностойкие (ХП) |
» |
735 |
875 |
Эмали химстойкие нетрещиностойкие (ХС, ХВ) |
» |
790 |
725 |
Эмали химстойкие трещиностойкие (ХП) |
» |
1000 |
900 |
Шпатлевка эпоксидная (ЭП) |
т |
2000 |
1200 |
Эмали эпоксидные (ЭП) |
» |
1850 |
1210 |
Проволока цинковая (порошок) |
» |
1200 |
230 |
Проволока алюминиевая (порошок) |
» |
1100 |
700 |
4. Антикоррозионные защитные покрытия |
|
|
|
Металлизация закладных деталей и арматуры |
руб/т |
170 |
- |
Защита закладных деталей лакокрасочными и другими неметаллическими покрытиями |
» |
50 |
- |
Гидрофобизация бетонной поверхности |
руб/м2 |
0,32 |
- |
Огрунтовка бетонной поверхности (1 слой): |
|
|
|
а) химстойкими нетрещиностойкими лаками (ХВ, ХС) |
» |
0,15 |
- |
б) химстойкими трещиностойкими лаками (ХП) |
» |
0,23 |
- |
в) эпоксидной грунт-шпатлевкой |
» |
0,3 |
- |
Нанесение покрытий на огрунтованные бетонные поверхности (1 слой)*: |
|
|
|
а) химстойкими нетрещиностойкими эмалями (ХВ, ХС) |
» |
0,14 |
- |
б) химстойкими трещиностойкими эмалями (ХП) |
» |
0,22 |
- |
в) эпоксидными эмалями (ЭП) |
» |
0,27 |
ѕ |
Оклейка химстойкими пленочными материалами (1 слой) |
» |
5 |
- |
* Толщина одного слоя лакокрасочного покрытия принята 20 мкм. |
Таблица 2
Ориентировочные данные (соотношения) для определения стоимости эксплуатационных затрат основных строительных конструкций в агрессивных средах
Строительные конструкции |
Капитальный ремонт Ск.р/Сд |
Возобновление защиты от коррозии Сз.к/Сз |
Элементы фундаментов |
1,03 |
1,15 |
Колонны, стойки |
0,96 |
1,2 |
Фермы, балки, ригели, прогоны и связи |
0,55 |
1,25 |
Стеновые панели |
0,66 |
1,1 |
Плиты перекрытий и покрытий (без учета кровли) |
0,47 |
1,25 |
Примечание. Сд - стоимость строительных конструкций «в деле» без защиты от коррозии (по усредненным показателям): Ск.р - затраты на один капитальный ремонт строительных конструкций; Сз - затраты на первоначальную защиту конструкций от коррозии; Сз.к - затраты, связанные с возобновлением антикоррозионной защиты при эксплуатации конструкций. |
Таблица 3
Ориентировочная продолжительность капитального ремонта железобетонных конструкций (на 1 м бетона конструкций)
Конструкции |
Продолжительность капитального ремонта в |
|
днях |
годах |
Фундаменты |
2,5 |
0,01 |
Колонны, стойки, стены |
3 |
0,012 |
Фермы, балки, ригели, прогоны |
3,5 |
0,013 |
Плиты покрытий и перекрытий |
4 |
0,015 |
Таблица 4
Ориентировочная стоимость производственных зданий и размещенного в них технологического оборудования, простой которого возможен при производстве капитального ремонта строительных конструкций
(на 1 м2 общей площади здания)
Отрасли промышленности |
Ориентировочная стоимость, руб. |
|
здания |
машин и оборудования |
Черная металлургия |
155 |
232 |
Цветная металлургия |
140 |
209 |
Химическая и нефтехимическая |
128 |
148 |
Машиностроение и металлообработка |
100 |
102 |
Деревообрабатывающая и целлюлозно-бумажная |
93 |
110 |
Строительных материалов |
101 |
95 |
Легкая промышленность |
102 |
97 |
Пищевая промышленность |
103 |
98 |
Прочие отрасли |
104 |
102 |
Примечание. Площадь здания и доля технологического оборудования, простаивающего во время капитального ремонта строительных конструкций, определяются по данным конкретного объекта и опыта эксплуатации производственных зданий аналогичного назначения.
|
Таблица 5
Значения суммарных коэффициентов m для приведения разновременных эксплуатационных затрат и издержек
Периодичность осуществления разновременных затрат, |
Нормативный (расчетный) срок службы зданий или сооружений Тс в годах |
лет |
30 |
40 |
50 |
60 |
70 |
80 |
90 |
100 |
1 |
9,363 |
9,747 |
9,9 |
9,945 |
9,965 |
9,975 |
9,985 |
9,995 |
2 |
4,428 |
4,629 |
4,706 |
4,733 |
4,743 |
4,748 |
4,753 |
4,758 |
3 |
2,788 |
2,944 |
2,985 |
3,001 |
3,009 |
3,012 |
3,015 |
3,019 |
4 |
2,003 |
2,082 |
2,129 |
2,14 |
2,146 |
2,147 |
2,151 |
2,153 |
5 |
1,486 |
1,578 |
1,613 |
1,626 |
1,63 |
1,632 |
1,634 |
l,636 |
6 |
1,163 |
1,252 |
1,28 |
1,285 |
1,289 |
1,291 |
1,292 |
l,294 |
7 |
0,98 |
1,015 |
1,042 |
1,046 |
1,048 |
1,05 |
1,051 |
1,053 |
8 |
0,784 |
0,831 |
0,863 |
0,871 |
0,873 |
0,874 |
0,876 |
0,878 |
9 |
0,680 |
0,712 |
0,725 |
0,73 |
0,732 |
0,733 |
0,734 |
0,736 |
10 |
0,534 |
0,591 |
0,613 |
0,621 |
0,623 |
0,624 |
0,625 |
0,626 |
11 |
0,473 |
0,516 |
0,531 |
0,536 |
0,538 |
0,539 |
0,54 |
0,541 |
12 |
0,419 |
0,451 |
0,461 |
0,461 |
0,463 |
0,464 |
0,465 |
0,466 |
13 |
0,374 |
0,398 |
0,398 |
0,405 |
0,407 |
0,408 |
0,408 |
0,409 |
14 |
0,332 |
0,332 |
0,350 |
0,354 |
0,354 |
0,355 |
0,356 |
0,357 |
15 |
0,239 |
0,296 |
0,309 |
0,310 |
0,311 |
0,312 |
0,312 |
0,313 |
16 |
0,217 |
0,264 |
0,274 |
0,274 |
0,276 |
0,276 |
0,277 |
0,278 |
17 |
0,198 |
0,237 |
0,237 |
0,244 |
0,246 |
0,246 |
0,247 |
0,247 |
18 |
0,18 |
0,212 |
0,212 |
0,217 |
0,217 |
0,218 |
0,218 |
0,219 |
19 |
0,163 |
0,189 |
0,189 |
0,193 |
0,193 |
0,194 |
0,194 |
0,195 |
20 |
0,149 |
0,149 |
0,17 |
0,171 |
0,173 |
0,173 |
0,174 |
0,174 |
21 |
0,135 |
0,135 |
0,153 |
0,153 |
0,155 |
0,155 |
0,156 |
0,156 |
22 |
0,123 |
0,123 |
0,138 |
0,138 |
0,14 |
0,14 |
0,141 |
0,141 |
23 |
0,111 |
0,111 |
0,123 |
0,123 |
0,125 |
0,125 |
0,125 |
0,126 |
24 |
0,101 |
0,101 |
0,111 |
0,111 |
0,111 |
0,112 |
0,112 |
0,113 |
25 |
0,092 |
0,092 |
0,092 |
0,1 |
0,1 |
0,101 |
0,101 |
0,101 |
Примечание. Величина m при промежуточных значениях Tс принимается по прямой интерполяции. |
Предыдущая часть |
К оглавлению
| Следующая часть
|